About Us
How we are using cutting-edge technologies to create safe, secure logistics equipment
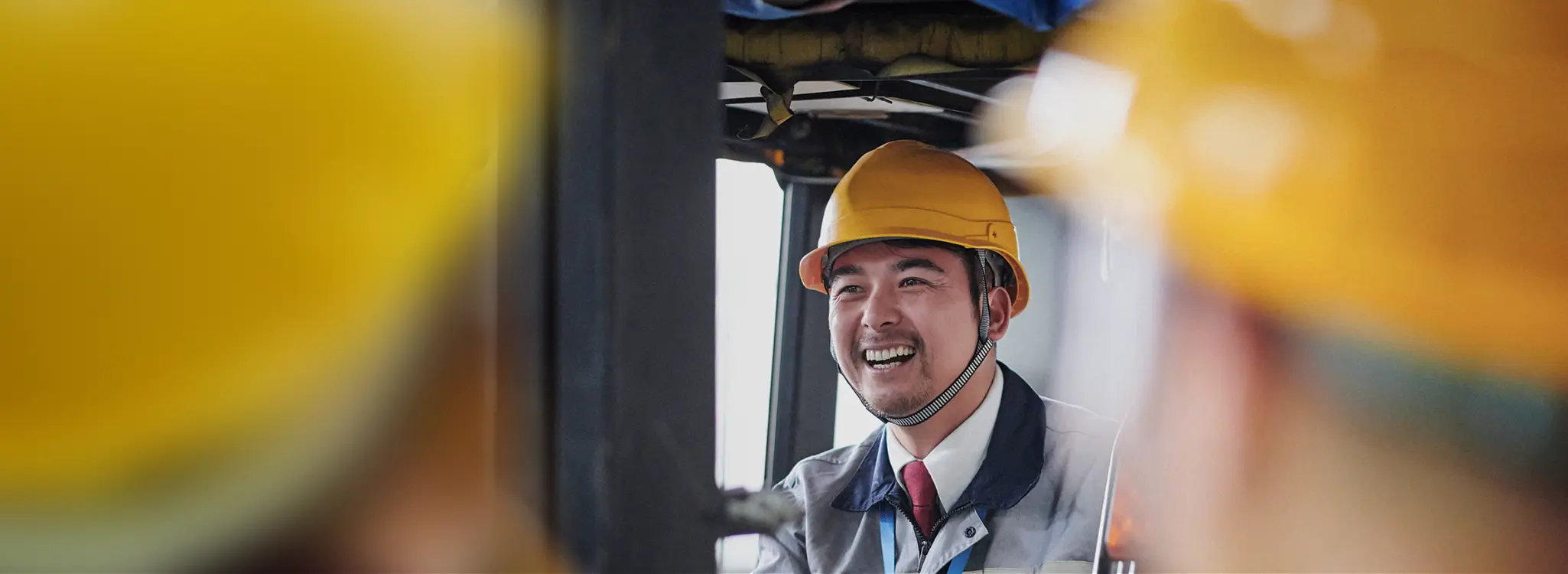
Industrial accidents involving forklifts put operators and workers at risk; the number of forklift accidents in Japan has remained at the relatively high level of about 2,000 annually, with fatal accidents totaling between 20 and 30 per year. Collisions and other accidents involving drivers that occur due to lack of safety checks, and entanglement accidents occurring during turns, are not uncommon, and a need exists to create safer work environments.
On the hardware side, we build on our track record and expertise with vehicles by installing safety support systems that incorporate artificial intelligence and other advanced technologies as well as various other safety features. On the software side, we provide safety awareness training through safety seminars and by providing safety tools.
We are committed to eliminating forklift accidents and contributing to safer working environments for our customers.
Trend in Number of Forklift Injuries and Fatalities in Japan
Initiatives
New S-Assist options for the ALESIS Counterbalanced Electric Forklift
Developing and offering products that reduce the stress associated with driving operations and help make safer work environments
In the belief that all operations can be performed safely and that anyone can easily operate our equipment, we provide products incorporating features carefully selected for safety and security. In 2022, we launched new S-Assist options for the ALESIS Counterbalanced Electric Forklift; these features safely and comfortably support driving operations for the benefit of the operator.
The two outstanding features of these options are Hill Stop Assist and Speed Control Assist. Hill Stop Assist prevents the vehicle from rolling backward when the operator switches between the accelerator and the brake, contributing to easy and safe starting on a slope.
Speed Control Assist is a proprietary feature that maintains a constant speed as the operator is lightly stepping on the accelerator. We have received positive comments from customers who praise this feature for enabling the operator to concentrate on the surroundings without being distracted by accelerator operation.
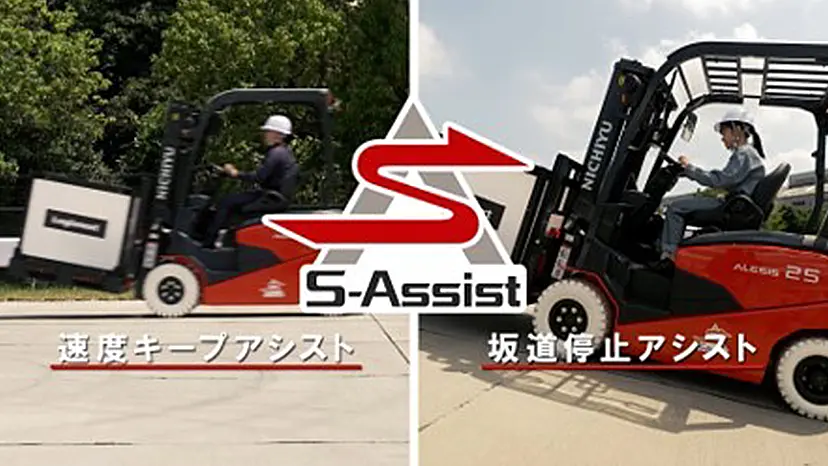
Our goal is to develop forklifts anybody can use easily in safety and with peace of mind.
I am responsible for developing the control software for the ALESIS forklift, and in this project my role was to develop controls for the S-Assist functions. This forklift was a model that had already been launched, and making sweeping changes to the driving controls could potentially have led to customer injuries, so our plan was to maintain the ease of driving as much as possible, but with a control method that would add the assistive functions.
Customers that have used S-Assist have praised how easy forklifts fitted with the technology are to operate compared to conventional ones; I’m very pleased with the positive feedback. Next, I hope we can add S-Assist functions to our other electric forklifts. I will also be working to develop new assistive features, such as those that help drivers avoid collisions.
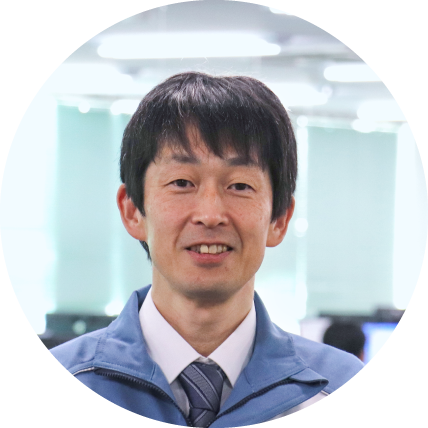
Engineering Headquarters New Product and Component
Development Division
Component Engineering Department Acting Manager
Masaki Nakada(Position as of April 2024)
*These comments represent opinions, job roles, and departmental affiliations that were correct at the time.
OmniEye® AI-powered human detection system & regenerative brake controls
Developing options to monitor vehicle blind spots and control braking, stopping, and moving off
OmniEye® is a system developed by Regulus Co., Ltd. that can use AI to detect the presence of human, and is an optional device that scans the equipped vehicle’s surroundings, using two cameras placed front and back, and warns the operator if it detects someone so as to prevent collisions before they can occur. With Regulus’ assistance, we have developed a vehicle fitted with regenerative brake controls as a special model of our electric ALESIS forklift.
This not only gives the user warnings, it can support collision avoidance by having the forklift apply its regenerative brakes when it detects someone nearby, or come to a complete stop if very close, and slow down at a certain distance if necessary.
- * OmniEye®is a registered trademark of Regulus Co., Ltd.
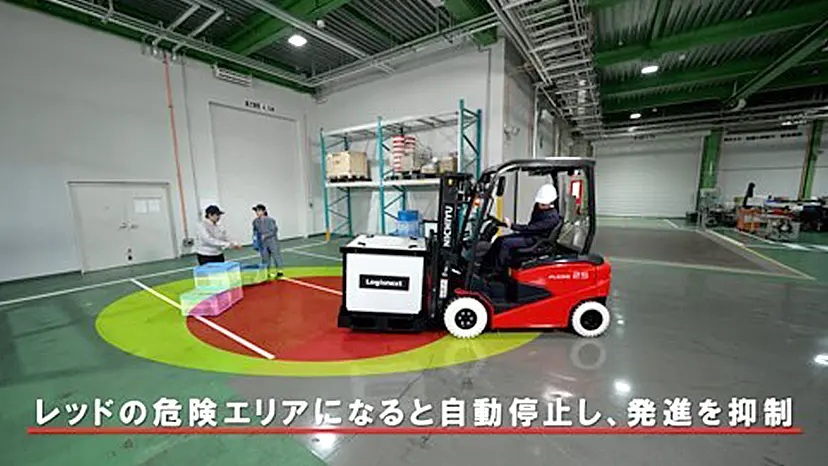
Customer feedback on accident prevention led to us developing this new product.
The trigger for this project was the consultations we received from customers we sell to about measures to prevent incidents where workers near forklifts are caught in the forklift. Working with related departments within Logisnext, we were able to create forklifts that are linked to the human-detecting cameras of the OmniEye® system so that when the cameras recognize a human in close proximity, the forklift automatically stops. We were able to verify this through repeated trials at customers’ sites. Of the challenges that faced us, one particularly difficult aspect was trying to fine-tune the responsiveness of the regenerative brakes so that they would automatically stop safely after detecting someone, not just slam on the brakes.
We were able to first announce the new model at an international event in the autumn of 2023, and soon afterwards we were inundated with inquiries from customers and requests to come to their sites to demonstrate the technology. Feedback for the equipment was very positive, and I think it can make a real contribution to eliminating accidents. In the future, we will continue our efforts to respond our expectations and commercialize toward forklift accident countermeasures in a short period of time, and hope to meet the expectations of “Mitsubishi Logisnext Fans” by delivering safe and secure products.
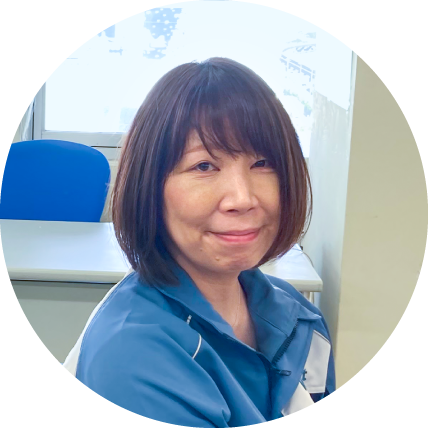
Domestic Sales and Marketing Headquarters National Account Sales and Special Vehicle Sales Support Division Assistant Manager
Yuki Hikita(Position as of April 2024)
*These comments represent opinions, job roles, and departmental affiliations that were correct at the time.
By listening to feedback, we are coming up with designs that exceed our customers’ expectations.
In this project, I was in charge of designing the electrical components and developing the software. I became involved in the project because my usual role is to design special models, such as creating safety features suited to customers’ sites.
With fitting forklifts with AI-powered cameras and human detection systems, the biggest obstacle was to simultaneously ensure both site safety and productivity. When we visited customers’ sites and received direct feedback, we realized that the key to our success would come down to whether we could optimize the responsiveness of the regenerative brakes. I am incredibly proud that we were able to meet the wishes of our customers for optimal responsiveness controls by adding deceleration functions to kick in when approaching someone, not just coming to a complete, sudden halt when very close. In the future, I would like us to continue incorporating the latest technologies while striving alongside our customers to resolve worksite issues.
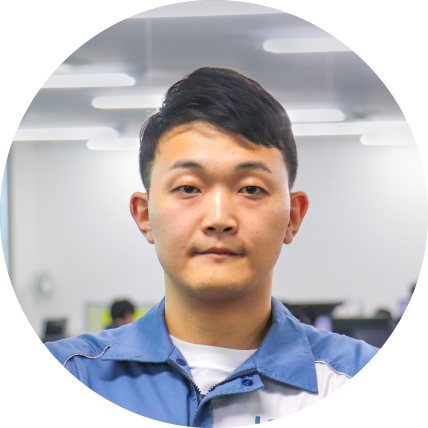
Engineering Headquarters Products Design Division Forklift Custom Design Department
Kangtae Park(Position as of April 2024)
*These comments represent opinions, job roles, and departmental affiliations that were correct at the time.