Providing Automation Systems for Customers
Providing unmanned and labor-saving products
Against the backdrop of rapidly growing labor shortages, we are developing safe, eco-friendly, and high-performance automated guided vehicles (AGVs) and automated guided forklifts (AGFs) to meet the need for automation at logistics sites.
In June 2022, we jointly developed the PLATTER Auto Forklift with a freezer warehouse specification (for 1.5 to 3.0 tonne models). This laser-guided automated forklift (laserguided AGF), jointly developed with Nichirei Logistics Group Inc., can operate in freezer warehouses at temperatures as low as -25℃.
Because fog and condensation can be obstacles to laser-guided AGFs in the -30℃ class when operating in refrigerated warehouses, we incorporated specialized components: those that can accommodate a refrigerated environment, which we developed for our conventional AGFs; and electrical components and sensors appropriate for -30℃ class equipment. After conducting demonstration tests with vehicles incorporating corrosion-resistance features, we achieved the commercialization of Japan’s first laser-guided AGF that does not require the laying of magnetic guides on the floor along the operating route.
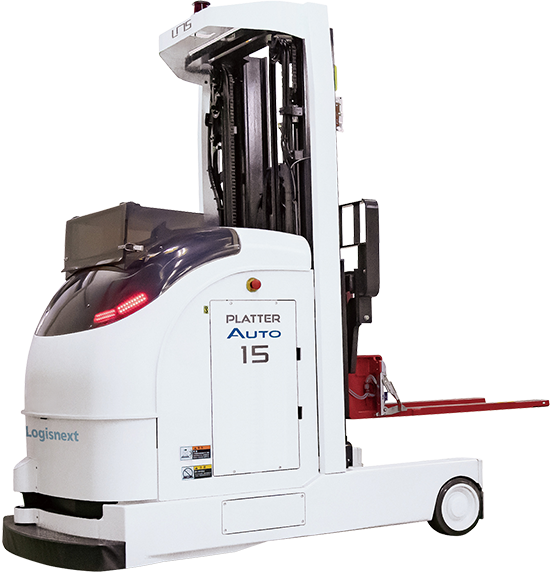
(1.5–3.0 tonnes)
Responding to global demand for automation
The AGV ACT (Automated Compact Truck), developed by Mitsubishi Logisnext Europe Oy in Finland, a European Group company, began accepting orders in March 2023 and is now available in Europe, North America, and Asia. Recognized for its exceptional design, it has won two of the world’s top three design accolades: the Red Dot Design Award and the iF Design Award for FY2024.
In September 2023, Rocrich AGV Solutions (Rocrich) commenced operations as a joint venture in the AGV business for the North American market. This new company was established through an equal partnership between Mitsubishi Logisnext Americas Inc., a U.S.-based Group company, and Jungheinrich AG, a German manufacturer specializing in general logistics equipment. Leveraging the extensive expertise of both companies in automated logistics solutions, Rocrich aims to enhance support and satisfaction for existing customers while accelerating the acquisition of new clients in the region.
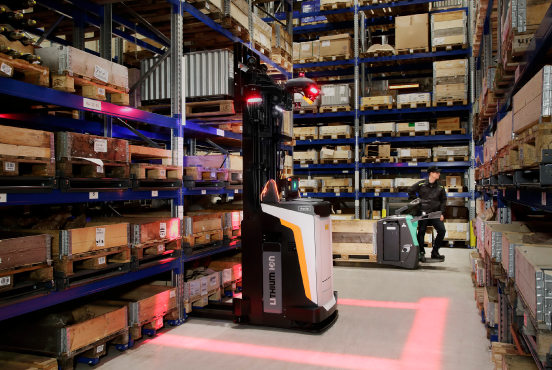
Using collaborations and alliances to promote and accelerate the digital transformation
In order to meet the growing need for automation, we are actively collaborating and forming business alliances with other companies.
We are manufacturing automated forklifts by installing automatic control equipment manufactured by Rapyuta Robotics Co., Ltd., with whom we have concluded a business alliance, in our electric forklifts.
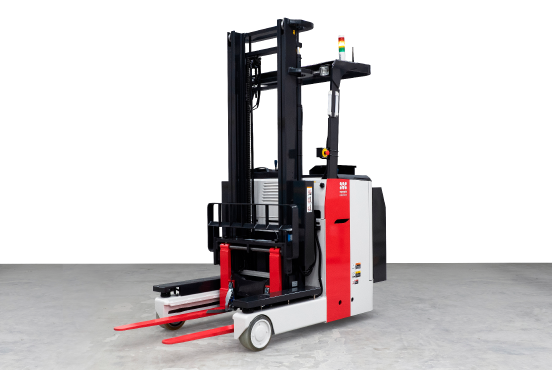
Moreover, we are developing automated picking solutions incorporating the ΣSynX (“Sigma Synx”) solution concept currently under development by Mitsubishi Heavy Industries, Ltd. Since AGFs and AGVs do not require large-scale modifications such as the installation of embedded floor guidance systems, they can be introduced into multitenant logistics facilities, which are currently becoming mainstream, and can easily accommodate sudden changes in warehouse layouts.
Participating in demonstration tests intended to address societal challenges
Moreover, since November 2022, Mitsubishi Heavy Industries, Ltd. and the Kirin Group have been participating in a joint demonstration of an automated picking solution. Within the Kirin Group, automation is steadily being introduced on production floors, but logistics in the company’s warehouses continues to rely heavily on manual labor and use of manned forklift trucks. The need to improve the work environment, especially through measures for picking heavy loads and rectifying the shortage of logistics operators, poses significant challenges.
In order to improve efficiency, the MHI Group’s automated picking solutions, automation systems, and intelligence can be introduced into picking processes that were previously performed by workers themselves. The combination of optimized engines and an integrated control system, all developed in-house, are enabling efficient coordination of multiple automated guided forklifts (AGFs) and automated guided vehicles (AGVs). This results in fewer picking and transfer operations, optimized picking processing, and higher throughput.
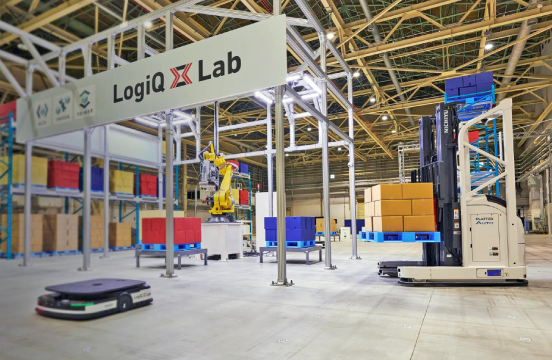