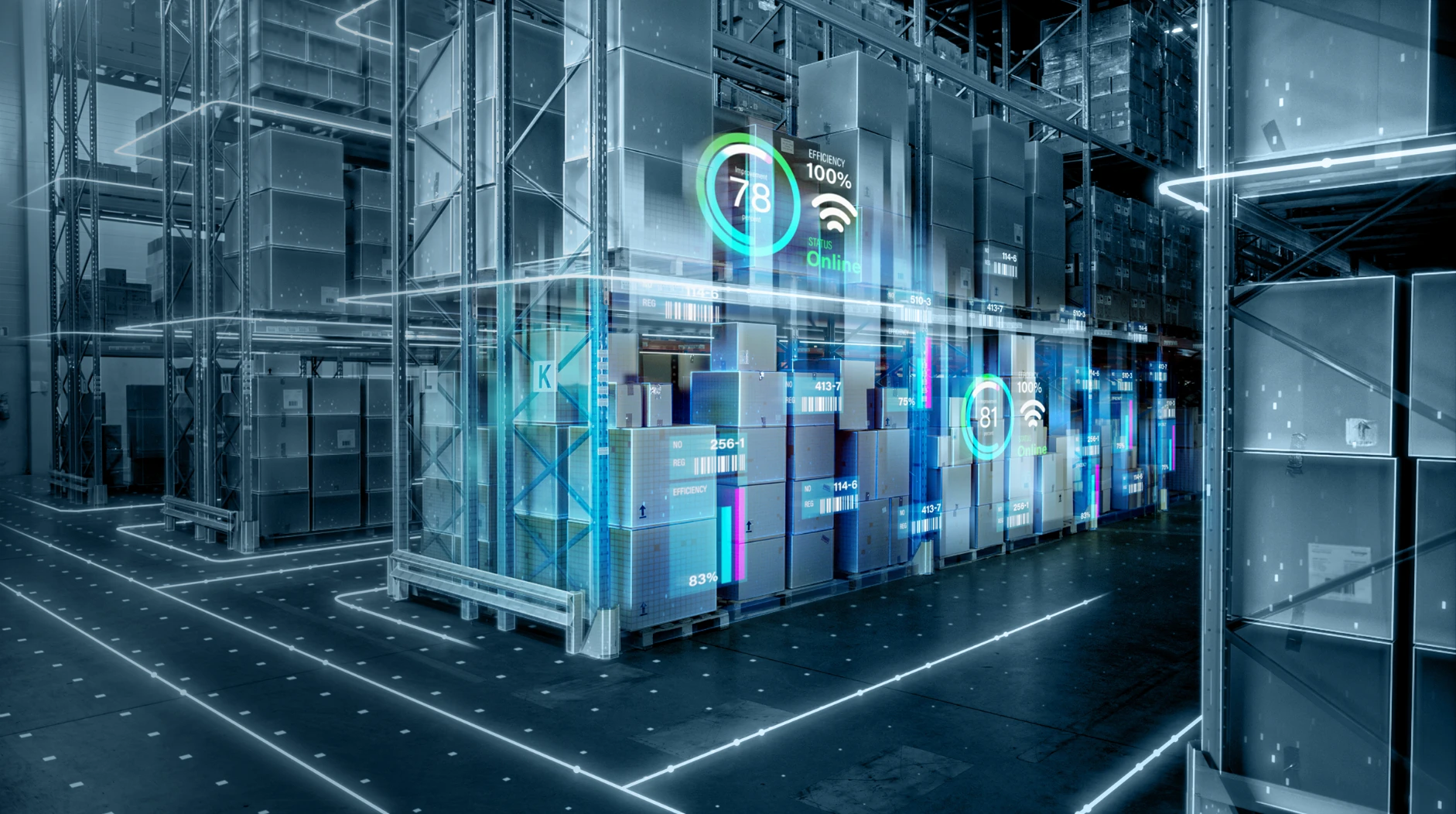
Core Technologies
Mitsubishi Logisnext, as the pioneer that developed the world’s first unmanned forklift, uses its original core technologies and wealth of expertise to create innovative solutions in the field of logistics system automation and labor-savings. It also takes advantage of the combined strengths of the MHI Group to also help resolve societal issues and contribute to regional revitalization.
Automation/unmanned operations technologies
Our automation/unmanned operations technologies, which we have been cultivating since our predecessor Nichiyu developed its own automated guided vehicle (AGV) in 1970, form one category of our core technologies. We now possess solutions that consider factors such as efficiency, but also workplace safety and security, and ease of introduction and use.
PLATTER Auto H,
able to transport and place items as well as a manned forklift
Our PLATTER Auto H model is a dedicated automated guided forklift (AGF) that can support this new age of logistics systems by meeting the automation needs that are growing in the logistics and warehousing markets.
This model can handle loading, unloading, and transporting tasks even more efficiently than our standard AGFs, with performance to rival a manned forklift. One characteristic is that it uses the very latest laser guidance systems so it can move items with the same rack layout as manned forklifts without the need to make alterations to the floor surface.
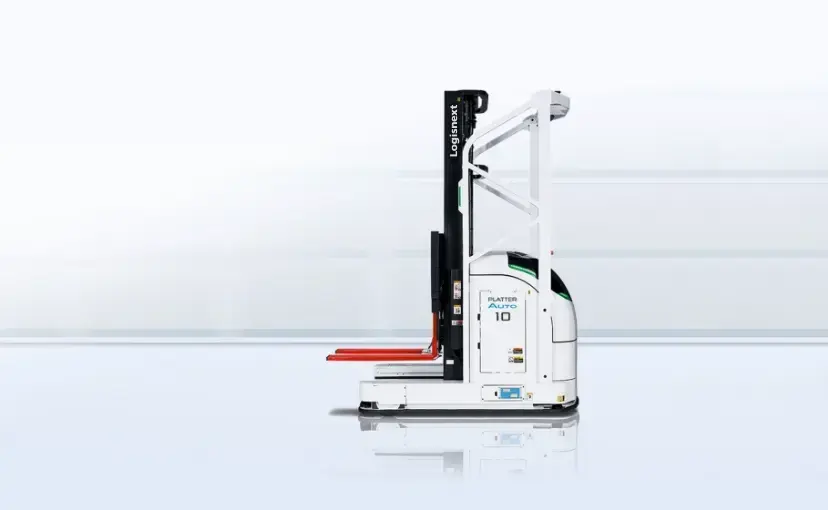
Autonomous/intelligent solutions
By creating automated, autonomous systems that synchronize and coordinate various mechanical systems, we will help to address issues of manpower shortages and labor-savings, solutions for which are expected to be in increasingly high demand in the future.
Automated solutions centered on unmanned forklifts and picking expertise
The automated picking solutions that MHI and Mitsubishi Logisnext offer are systems that use one of the core technologies—ΣSynX—for automated, intelligent picking work that considers workers and efficiency. Through the optimized engines and control systems that we have developed, we are optimizing picking work and improving throughput. Our efforts also help to resolve issues such as labor shortages, the hard work of dealing with heavy items, and human error.
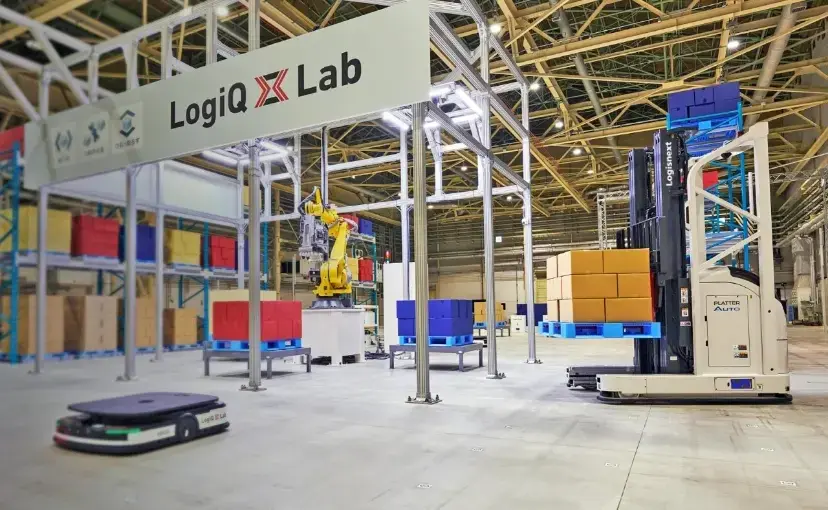
contributing to more efficient logistics through unmanned forklifts, etc. ΣSynX
ΣSynX (“sigma syncs”) is MHI’s standard platform for synchronizing and coordinating various types of machinery systems. It consolidates a lot of digital technologies that enable optimized operation by adding intelligence to machinery systems.
Watch the video to find out more
Product design capabilities
With multiple development sites located inside and outside Japan, one of our strengths is our product design capabilities, which are based on regional needs in different parts of the world.
The pursuit of designs that help connect logistics worksites and vehicles to allow drivers to face their daily logistics work positively
We have given form to a number of key concepts: a user experience that makes the user feel at one with their vehicle, comfort that considers the sensations of passengers, durability and serviceability that does not interrupt work on sites, environmental performance that is kind to the environment, and—more important than anything else—safety.
Styling performance
When it comes to aspects such as visibility from the driver’s seat or operability, our design philosophy is that the vehicle should match the operator, not the other way around, and by doing so we design in a positive relationship between the two.
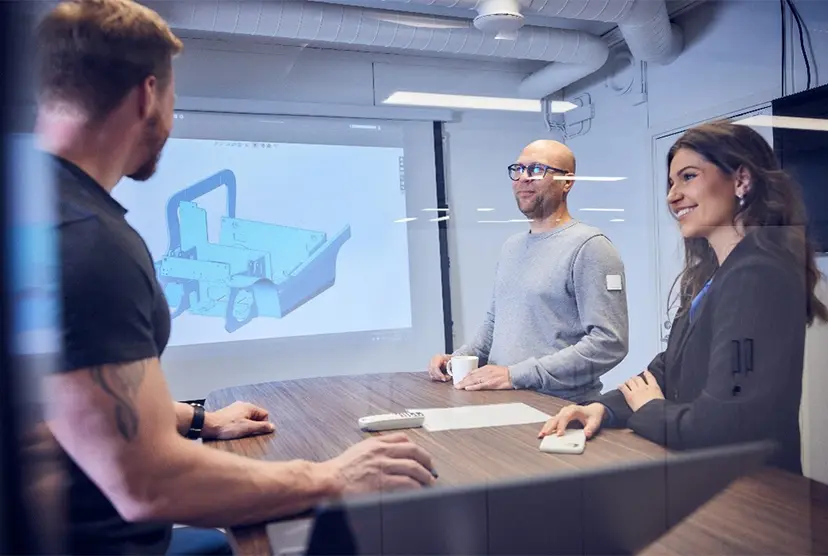
Key component development capabilities
During the development of engine-powered vehicles, power is not the only consideration. Environmental performance is also required to clear each country’s emissions standards. We use components that our Group has itself developed and produced. By utilizing and optimizing the technologies we have developed through our work with passenger vehicles, we have achieved engines with excellent response and torque.
Powerline full-floating design for class-leading low vibration levels
We utilize a powerline full-float design that makes use of the technologies we have built up in passenger vehicles. The class-leading low vibration levels help reduce fatigue for the operator and offer a more comfortable working environment.
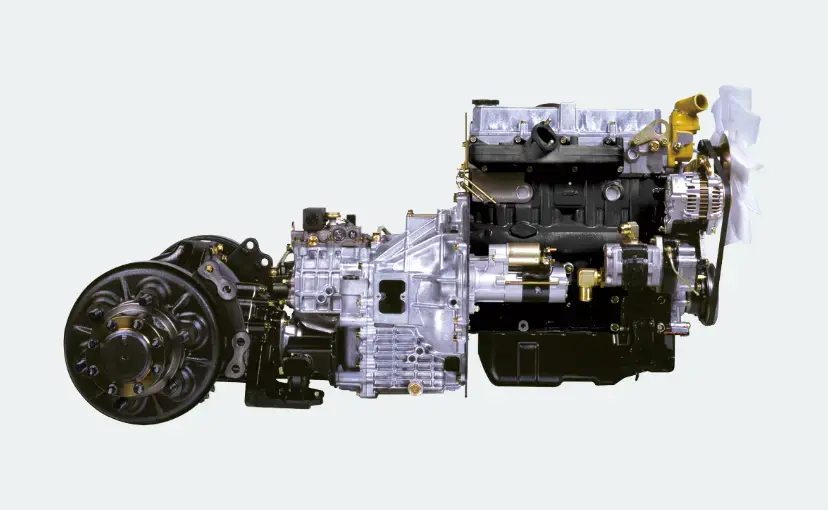
Environmental/safety enhancement technologies
To ensure safe, secure forklift operations, as well as the functions of the forklift itself, the operator needs to check safety, such as through visual inspections. We have the system solutions needed to detect humans, as distinct from other obstacles, through our own proprietary AI-powered image recognition technologies.
Good Finder, AI-powered human detection system
Good Finder is an AI-powered human detection system that brings together technologies from Mitsubishi Logisnext, with our excellence automotive technologies, and Mitsubishi Heavy Industries, with its high-resolution processing and detection technologies. Through video footage from cameras fitted on the forklift, the system can detect humans quickly and with a high degree of accuracy and notify the user of the nearby presence of a person through a warning alarm noise and LED.
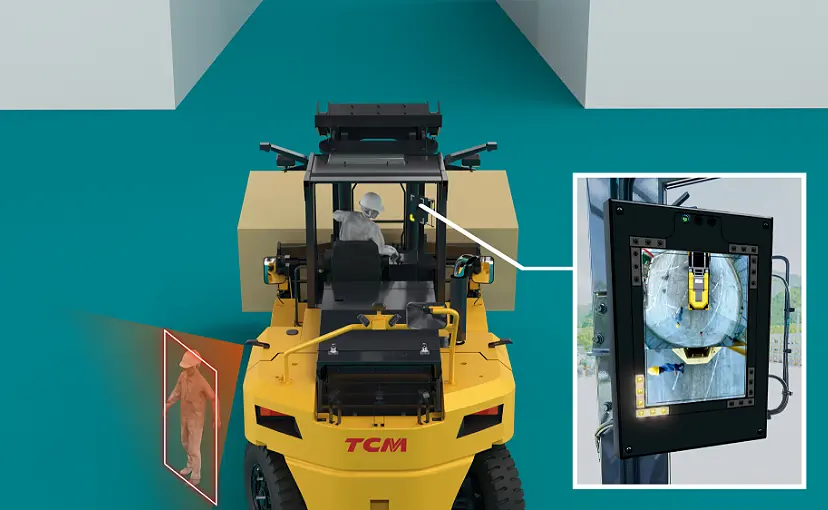